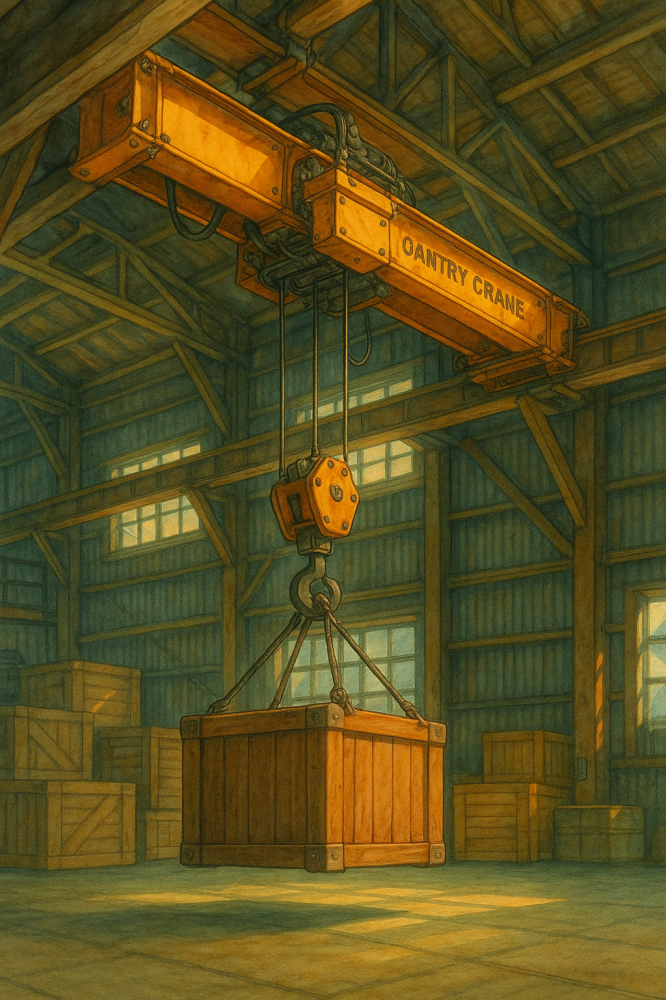
クレーンやバランサーを何度も設計してきた私にとって、吊り具の設計は毎回「難しさ」と「楽しさ」が同居する仕事でした。クレーン本体やバランサーの構造設計ももちろん重要ですが、実際にワークを把持(はじ)し、持ち上げ、移動させる“吊り具”こそ、現場で最終的にものを掴んでいる部分です。そのため、安全面や作業性が直接的に問われるのがこの吊り具になります。
絶対に落下させないための安全装置
吊り具の設計で第一に考えるべきは、「絶対にワークを落下させない」ことです。落下は作業者の安全や生産ライン全体に深刻な影響を及ぼすばかりでなく、企業としての信頼にも関わります。
私が設計していたときも、停電などの予期せぬトラブルが起きたときに、どのように安全を確保するかを常に頭に置いていました。具体的には、バランサーやクレーンの動力が途切れた際に自動でロックがかかる機構や、エアシリンダーがダウンしても保持力を失わないようにする逆止弁付きの回路などが挙げられます。また、複数の安全装置を用意し、どれかひとつが不具合を起こしても落下しない“フェイルセーフ”設計を取り入れることも大切です。
衝撃や乱暴な操作に耐える強度設計
現場では、必ずしも操作マニュアルどおりに丁寧な取り扱いがされるとは限りません。作業者が焦っていたり、作業環境が狭かったりすると、吊り具をワークや周囲の設備にぶつけてしまうこともあります。
だからこそ、吊り具には衝撃に耐えうる強度が必要となります。「想定外の力」が加わった場合でも簡単に破損しない設計を行うことで、現場のトラブルを大幅に減らすことができるでしょう。ここでは、材料選定から部品同士の取り付け強度、溶接部の配置や寸法など、細かいところまでチェックが欠かせません。
慣性力と剛性によるタワミへの配慮
クレーンやバランサーで比較的ゆっくり動かす作業であっても、実際には停止・加速・減速といった動作の過程で慣性力が発生します。特に精密な位置決めや揺れを嫌う工程では、吊り具の剛性が重要になります。
剛性が低いと、ワークの移動時に振動やタワミが大きくなり、位置決めが難しくなるだけでなく、ワークの損傷リスクも高まります。したがって、設計段階で部材のたわみ量を予測して対策を打つことが不可欠です。必要に応じて、補強リブを追加したり、部材の肉厚を変更したりすることで剛性を向上させることができます。
操作方式の選択とユーザビリティ
吊り具の操作方式も、設計においてよく議論となるポイントです。チャック・アンチャックを手動で行うのか、それとも電気やエアを使ってボタン一つで行うのか。ボタンの配置ひとつをとっても、右利き・左利き、作業性、安全性など、現場の要望やオペレーターの慣れをしっかりヒアリングしたうえで決める必要があります。
たとえば、手動式の場合はシンプルな構造でコストを抑えられますが、作業者が複数人いる現場では誤操作や操作ミスが起きないように配慮しなければなりません。一方、自動化や半自動化によってボタン操作のみで着脱を行えるようにすれば、作業者の負担は軽くなりますが、構造が複雑になり、メンテナンスも増える可能性があります。
こうしたトレードオフをお客様としっかり打ち合わせ、試作やデモを通じて検証しながら進めることが大切です。
設計者に必要なマインド――寄り添う姿勢と問題解決力
クレーン、バランサー、そして吊り具。どの装置でも共通して言えるのは、エンドユーザーや作業者の立場に立って設計を進めることの重要性です。現場には、図面だけからは見えないヒントや課題が潜んでいます。実際に使う方が「ここが怖い」「ここでもう少しスペースが欲しい」「こんな風に操作できたらいいのに」と思う部分にこそ、設計者が解決すべき本質があります。
“安全性”“作業性”“コスト”“メンテナンス性”など、考慮すべき要素は多岐にわたりますが、そのすべてに対して「どうすれば目の前の人の不安や不便を解消できるか」を常に考える姿勢が必要です。最終的には、現場の声をしっかり受け止め、設計者の技術力や想像力を駆使して最適解を導き出す。これこそが吊り具設計の醍醐味であり、大きなやりがいだと思います。
吊り具の設計は、難易度が高いからこそ面白い世界です。安全に関わる重大な要素を担いつつ、細かな操作性や使い勝手も追求しなければなりません。お客様や作業者と同じ目線に立ち、難しい課題を一緒に解決しようとする姿勢が、最終的な仕上がりを大きく左右します。私自身、これまでの経験で得た学びと失敗を糧に、これからも「絶対に落下させない」「使いやすい」と自信を持って言える吊り具を生み出していきたいと思っています。